Annealing: The Rebirth of Steel
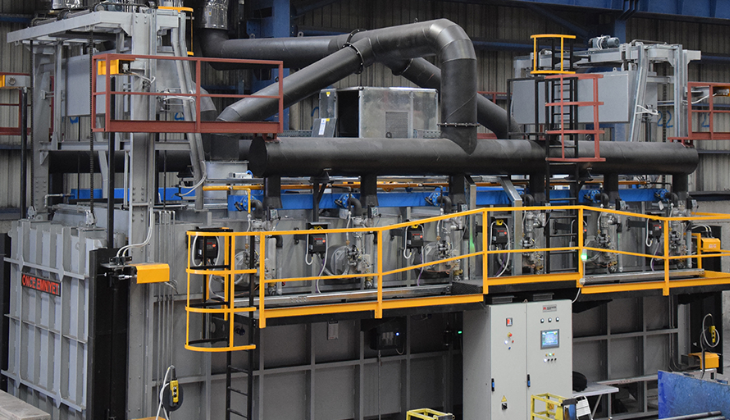
Annealing is a heat treatment process that involves heating metals to a specific temperature and then cooling them in a controlled manner to improve their internal structure and mechanical properties. This process enhances the machinability of metals, reduces internal stresses, and helps achieve specific material properties.
What Is the Purpose of Annealing?
- Reducing Internal Stresses
- Annealing eliminates internal stresses that develop during manufacturing and processing. This reduces the risk of cracking and fracture in the material.
- Improving Microstructure
- The annealing process refines the crystalline structure of the metal, leading to a more homogeneous composition. This enhances the mechanical properties of the material.
- Balancing Hardness and Ductility
- Annealing lowers the hardness of the material while increasing its ductility. This makes the metal easier to machine and shape.
Advantages of Annealing
✔ Enhanced Machinability
- By reducing hardness, annealing improves the machinability of metals, making manufacturing processes faster and more efficient.
✔ Elimination of Internal Stresses
- Annealing removes internal stresses caused by manufacturing and processing, reducing the risk of cracks and fractures.
✔ Improved Microstructure
- The process enhances the metal’s crystalline structure, leading to better mechanical properties.
✔ Optimized Hardness and Ductility
- Annealing makes metals softer and more ductile, facilitating machining and forming operations.
Types of Annealing
1. Normalizing Annealing
Normalizing annealing involves heating steel to a specific temperature and then cooling it in air. This process ensures a uniform microstructure and improves the mechanical properties of the steel.
Key Benefits:
- Homogeneous Microstructure: Ensures uniform internal structure.
- Increased Durability: Enhances mechanical properties and strength.
- Improved Machinability: Facilitates processing.
2. Stress Relief Annealing
Stress relief annealing is performed at low temperatures, followed by slow cooling to eliminate internal stresses. It is often applied after welding, cold working, or forging.
Key Benefits:
- Prevents Stress-Related Cracking: Reduces residual stresses.
- Dimensional Stability: Maintains dimensional accuracy.
- Extended Service Life: Increases the lifespan of steel components.
3. Spheroidizing Annealing
Spheroidizing annealing promotes the formation of spherical carbides in steel, making it particularly useful for high-carbon steels.
Key Benefits:
- Improved Machinability: Enhances ease of cutting and shaping.
- Higher Wear Resistance: Spherical carbides increase wear resistance.
- Reduced Brittleness: Lowers the likelihood of cracking.
4. Soft Annealing
Soft annealing involves heating steel to a specific temperature and then slowly cooling it to reduce hardness. This process makes the steel easier to machine.
Key Benefits:
- Increased Machinability: Makes steel softer and easier to process.
- Reduction of Internal Stresses: Improves material stability.
- Enhanced Ductility: Increases flexibility and workability.
How Is the Annealing Process Performed?
1. Preparation Stage
- Material Selection: The type of steel to be annealed is determined (e.g., carbon steels, alloy steels).
- Cleaning: The surface of the steel is cleaned from dirt, oil, and oxides to ensure an effective process.
2. Heating Stage
- Heating Furnace: Steel is heated in a high-temperature-resistant furnace with precise temperature control.
- Heating Temperature: Typically ranges between 800-950°C, depending on the type of steel.
- Heating Time: Steel is held at the desired temperature for a specified period, depending on its thickness.
3. Soaking Stage
- Duration: The steel remains at the target temperature to allow for a uniform microstructure.
- Control: Temperature is maintained consistently for better homogeneity.
4. Cooling Stage
- Cooling Method: Steel can be cooled in air, inside the furnace, or in water, depending on the desired properties.
- Cooling Rate: Adjusted according to the steel’s requirements—slower cooling increases ductility, while faster cooling enhances hardness.
5. Final Inspections
- Microstructure Examination: The annealed steel is analyzed under a microscope to check if the desired microstructure has been achieved.
- Mechanical Testing: Hardness, ductility, and strength tests are performed to evaluate the success of the annealing process.
Industrial Applications of Annealing
✔ Automotive Industry: Used in engine components, transmission gears, and suspension systems.
✔ Aerospace Industry: Strengthens aircraft fuselage parts, engine components, and landing gear.
✔ Construction and Structural Materials: Enhances durability in steel beams, columns, and bridge components.
✔ Energy and Power Generation: Applied to turbine blades and shafts for high-strength applications.
Conclusion
Annealing is a heat treatment process that improves the internal structure and mechanical properties of metals by heating them to a specific temperature and cooling them in a controlled manner. This process enhances machinability, reduces internal stresses, and helps achieve desirable material characteristics.
Annealing is widely used in industries such as automotive, aerospace, construction, and energy, making metals more durable and workable.
Each type of annealing is designed to optimize specific properties of steel. Normalizing annealing ensures a homogeneous microstructure, stress relief annealing reduces internal stresses, spheroidizing annealing enhances carbide structure for better machinability, and soft annealing lowers hardness for improved workability. These processes enhance steel’s performance and durability, making them essential for industrial applications.