Alloy: A Revolution in the Steel Industry
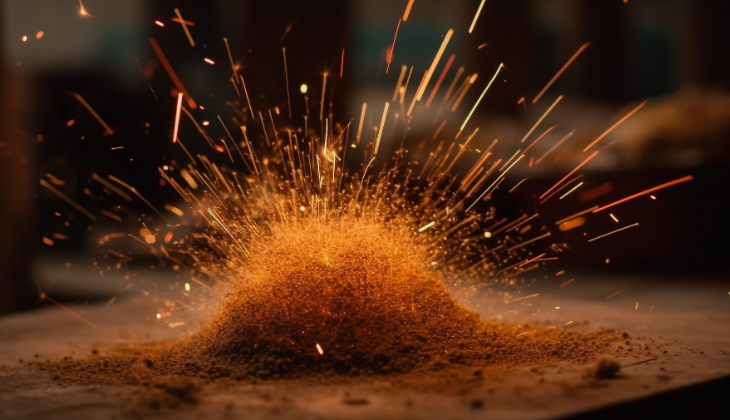
Have You Ever Wondered?
Would you like to learn how alloys have revolutionized the steel industry? Get ready for an exciting journey from start to finish!
Let's Begin!
The History of Alloys
The history of alloys dates back to the earliest periods of human civilization. This process began around 4000 BC with bronze (a mixture of copper and tin) and played a crucial role in the development of metalworking technology.
The First Alloy: Bronze
- Discovery: Discovered around 3500 BC in Mesopotamia.
- Impact: This discovery led to the beginning of the Bronze Age, marking a major revolution in human history.
What is an Alloy?
An alloy is a material formed by combining at least two or more elements, usually metals, in specific proportions. In the steel industry, steel alloys are created by adding elements to iron and carbon, enhancing their properties and performance. Many commonly used materials, such as steel, bronze, and brass, are actually alloys.
Why Was There a Need for Alloys?
Pure metals often fall short in certain applications. The need for alloying arose to improve metal properties and tailor them to specific requirements. The main objectives of alloying include:
- Increased Strength: Alloys enhance the strength of pure metals. For example, iron combined with carbon forms steel, which is significantly stronger than pure iron.
- Corrosion Resistance: Some alloys are made resistant to corrosion. Stainless steel, an alloy of iron, carbon, and chromium, is highly resistant to rust.
- Flexibility and Malleability: Alloys are often more flexible and malleable, providing a great advantage in manufacturing.
- Specialized Properties: Custom alloys can be developed to meet specific needs, such as electrical conductivity, magnetic properties, and high-temperature resistance.
Key Properties of Alloys
- Strength: The ability of a material to withstand applied forces. Alloys provide greater strength than pure metals.
- Hardness: The resistance of a material to surface deformation, such as indentation or scratching. Alloys directly impact hardness.
- Ductility and Toughness: Ductility is the ability of a material to deform without breaking, while toughness is its ability to absorb energy.
- Corrosion Resistance: The ability of a material to withstand environmental effects without degradation. Alloys can improve corrosion resistance.
- Machinability: Alloys can enhance the suitability of a material for cutting, drilling, or shaping processes.
Examples of Alloys
- Steel: Pure iron has low strength and corrosion resistance. When alloyed with carbon and other elements, steel gains increased strength and durability.
- Tool Steels: Achieve extreme hardness with the addition of tungsten and vanadium, making them ideal for cutting tools.
- Nickel-Based Alloys: Offer high ductility and toughness, making them suitable for extreme conditions.
- Stainless Steel: Contains chromium, providing excellent resistance to oxidation and corrosion.
- Copper and Aluminum Alloys: Known for high electrical and thermal conductivity, commonly used in electrical wiring.
- Aluminum Alloys: Preferred in the aerospace and automotive industries due to their low density.
- Invar (Nickel-Iron Alloy): Has a very low thermal expansion coefficient, making it ideal for precision measurement devices.
- Magnetic Steels: Iron-nickel alloys used in electric motors, generators, and transformers.
- Titanium Alloys: Withstand high temperatures, making them suitable for high-temperature applications.
- Aluminum and Copper Alloys: Easily machinable, making them useful for various industrial applications.
How Are Alloys Produced?
Alloys are created through melting and mixing processes. In the steel industry, this process involves:
- Melting
- Blast Furnaces: Iron ore, coke, and limestone are melted in blast furnaces.
- Steel Production: The resulting pig iron is processed in oxygen furnaces.
- Alloying
- Adding Elements: Carbon and other alloying elements are added to the molten metal.
- Mixing: The mixture is stirred until a homogeneous composition is achieved.
Common Alloying Elements
To enhance their properties, various alloying elements are added to steels, each contributing specific benefits:
- Carbon (C): Increases strength and hardness.
- Chromium (Cr): Improves corrosion resistance.
- Nickel (Ni): Enhances ductility and impact resistance.
- Molybdenum (Mo): Increases high-temperature strength.
- Manganese (Mn): Boosts hardness and wear resistance.
- Vanadium (V): Improves hardness and wear resistance.
- Silicon (Si): Enhances strength and hardness.
- Tungsten (W): Increases strength at high temperatures.
- Titanium (Ti): Improves strength and hardness.
- Aluminum (Al): Helps remove oxygen from steel, increasing purity.
- Boron (B): Enhances hardness and strength.
Alloy Examples and Their Applications
- Stainless Steel
- Applications: Kitchenware, medical devices, construction.
- Properties: Corrosion resistance, shiny surface.
- Tool Steels
- Applications: Cutting tools, molds, and press machines.
- Properties: High hardness, wear resistance.
- High-Strength Low-Alloy Steels (HSLA)
- Applications: Construction, automotive, maritime industries.
- Properties: High strength, low weight.
- Carbon Steel
- Applications: Construction bars, pipes, frames, and structural components.
- Properties: Varies in strength depending on carbon content, low production cost, easy machinability, and formability.
The Importance of Alloys in the Steel Industry
The steel industry has undergone a major transformation thanks to alloys. Alloys allow the production of more durable, flexible, and versatile steel products, providing innovative solutions across industries such as construction, automotive, and energy.
- Construction, automotive, and heavy machinery industries now benefit from high-strength and hardness requirements.
- Stainless steel is widely used in chemical plants, marine vessels, and food processing equipment due to its long lifespan.
- The automotive and aerospace industries now produce complex and precision-engineered parts.
- Power plants and energy infrastructure leverage high-performance alloys for extreme environments.
Alloys continue to shape the future of the steel industry, driving progress and innovation!